Rotary Vs Box Motion Flow Wrapper: What Is The Difference?
Packaging machinery plays a crucial role in ensuring products are safely and efficiently packaged. Flow wrappers are widely utilized in a variety of industries, including food, medicines, cosmetics, and hardware. Within the realm of flow wrapping, two primary types of machines are frequently discussed: box motion flow wrappers and rotary flow wrappers. Understanding the differences between these two can help businesses make informed decisions to optimize their packaging processes.
What is a Flow Wrapper?
Flow wrappers, also known as horizontal form-fill-seal (HFFS) machines, are designed to wrap products of various shapes and sizes in a continuous film.The film is fed from a roll, wrapped around the product, and sealed to create a protective and often aesthetically pleasing package. Flow wrapping offers several benefits, including high-speed operation, versatility, and efficient use of packaging materials.
Overview of Box Motion Flow Wrappers
Box motion flow wrappers are characterized by their distinctive sealing mechanism. Unlike rotary wrappers, the sealing jaws in box motion machines move in a straight line along the direction of the film flow (hence the term "box motion"). This allows the jaws to have a longer dwell time on the film, ensuring a secure and high-quality seal.
Advantages of Box Motion Flow Wrappers
Superior Seal Quality
The extended dwell time of the sealing jaws in box motion flow wrappers results in excellent seal integrity. This makes them ideal for packaging products that require hermetic seals, such as medical devices, perishable foods, and products with stringent barrier requirements.
Versatility with Film Types
Box motion wrappers can handle a wider range of film materials, including thicker and more complex laminates.This adaptability makes them appropriate for applications that require specialist films, such as those with strong barrier qualities.
Ideal for Heavy and Irregularly Shaped Products
The robust sealing mechanism of box motion wrappers allows them to handle heavier and irregularly shaped products more effectively. The precise control over the sealing process ensures that even challenging items are securely packaged.
Limitations of Box Motion Flow Wrappers
Slower Speeds
One of the primary limitations of box motion flow wrappers is their relatively slower operating speed compared to rotary flow wrappers. The longer dwell time, while beneficial for seal quality, results in lower throughput.
Higher Cost and Complexity
Box motion flow wrappers tend to be more expensive and complex due to their advanced sealing mechanisms. The initial investment and maintenance expenses may be higher, making them unsuitable for organizations with limited resources.
Overview of Rotary Flow Wrappers
Rotary flow wrappers, also known as rotary motion flow wrappers, utilize a continuous rotating movement of the sealing jaws. This design allows the machine to operate at higher speeds, making it suitable for high-volume packaging applications. The film is wrapped around the product, and the rotating jaws cut and seal the film in one continuous motion.
Advantages of Rotary Flow Wrappers
High-Speed Operation
Rotary flow wrappers are renowned for their ability to operate at high speeds, making them ideal for high-volume production lines. This capability significantly enhances productivity and efficiency, especially in industries with fast-moving consumer goods.
Lower Initial Costs
Compared to box motion flow wrappers, rotary flow wrappers are generally more cost-effective in terms of initial investment.Their simplified design and fewer moving parts lead to lower purchase and maintenance expenses.
Compact Footprint
Rotary flow wrappers typically have a more compact design, which can be advantageous for facilities with limited floor space. Their smaller footprint allows for easier integration into existing production lines.
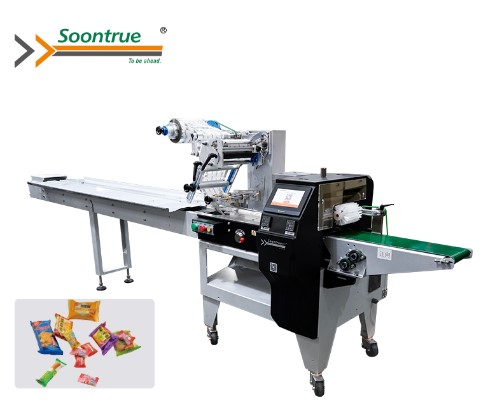
Limitations of Rotary Flow Wrappers
Limited Seal Quality
The continuous rotary motion results in shorter dwell times for the sealing jaws, which can affect the seal quality. This limitation makes rotary flow wrappers less suitable for products requiring hermetic seals or thicker packaging films.
Less Versatility with Film Types
Rotary flow wrappers may struggle with thicker and more complex films, limiting their versatility. They are best suited for applications that use standard packaging films and require moderate sealing.
Challenges with Irregularly Shaped Products
The design of rotary flow wrappers makes them less effective at handling irregularly shaped or heavy products. The continuous motion can lead to misalignment and inconsistent sealing for such items.
Key Considerations for Choosing Between Box Motion and Rotary Flow Wrappers
Product Type and Requirements
The nature of the product being packaged is a critical factor in choosing the appropriate flow wrapper. Products requiring high-quality, hermetic seals, such as medical supplies and perishable foods, are better suited for box motion flow wrappers. Conversely, standard consumer goods that can tolerate less robust seals are ideal candidates for rotary flow wrappers.
Production Volume
For operations with high production volumes, rotary flow wrappers offer a significant advantage due to their higher throughput.On the other hand, for lower volume production where seal integrity is paramount, box motion flow wrappers are the preferred choice.
Budget and Cost Considerations
Initial investment and operating expenditures are critical concerns. Rotary flow wrappers typically have a cheaper cost of entry and lower maintenance costs, making them appealing to budget-conscious enterprises. However, the higher initial investment in a box motion flow wrapper can be justified by the superior seal quality and versatility in handling different films and product types.
Space Constraints
The physical footprint of the machinery is another practical consideration. Rotary flow wrappers, with their compact design, are suitable for facilities with limited space. In contrast, box motion flow wrappers, which often require more room due to their complex sealing mechanisms, are better suited for larger production environments.
Film Material and Packaging Needs
The choice of film material and the specific packaging needs play a significant role in deciding between the two types of flow wrappers. Box motion wrappers may accept a broader range of film materials, including those that require longer dwell times for optimal sealing. Rotary wrappers, however, are more efficient with standard films and simpler packaging requirements.
Conclusion
Choosing between a box motion flow wrapper and a rotary flow wrapper depends on a variety of factors, including product type, production volume, budget, space constraints, and packaging requirements.If you are looking for a box motion flow wrapper or a rotary flow wrapper, Soontrue can help you. We are devoted to offer a wide range of food packing machines. Click the link to browse our website for more product details now!